Переоборудование бензиновых впрысковых двигателей на газ
Для повышения топливной экономичности, улучшения динамики и особенно для снижения вредных выбросов выхлопных газов двигателей кандидат технических наук, профессор Московского автомобильно‑дорожного института Ю. В. Панов в результате научных исследований и многолетнего опыта работы с газобаллонной аппаратурой предлагает перевод впрысковых автомобилей на газ сжиженный нефтяной.
Впрысковая бензиновая система питания (рис. 22) существенно отличается от карбюраторных и механических впрысковых.
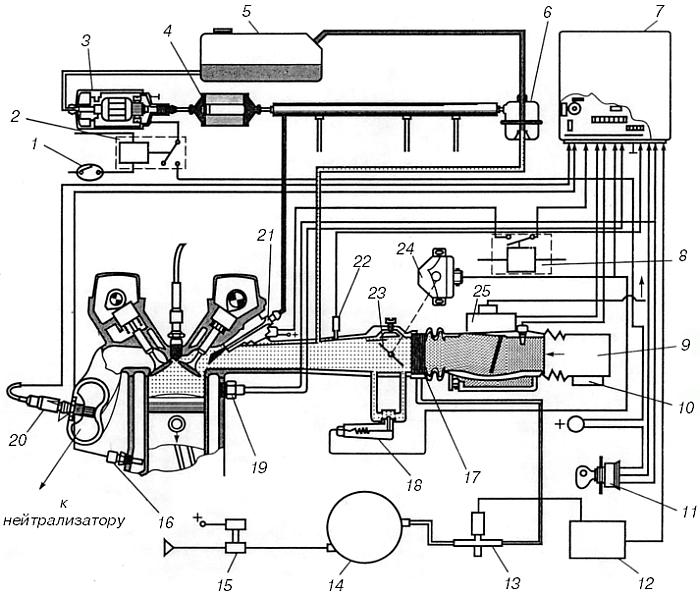
Рис. 22. Система многоточечного впрыска: 1 – переключатель «Бензин‑Газ»; 2 – реле включения бензонасоса; 3 – бензонасос; 4 – топливный фильтр; 5 – бензобак; 6 – регулятор давления; 7 – ЭБУ; 8 – дополнительное реле выключения инжекторов; 9 – корпус воздушного фильтра; 10 – предохранительный клапан; 11 – замок зажигания; 12 – согласующий электронный блок; 13 – газовый дозатор; 14 – редуктор низкого давления (газовый); 15 – электромагнитный клапан‑фильтр; 16 – датчик температуры охлаждающей жидкости; 17 – газовый смеситель; 18 – клапан холостого хода; 19 – датчик детонации; 20 – лямбда‑зонд; 21 – бензиновый инжектор; 22 – датчик положения дроссельной заслонки; 23 – дроссельная заслонка; 24 – шаговый электродвигатель; 25 – расходомер воздуха.
Подготовкой смеси и подачей топлива в инжекторной системе управляет бортовой компьютер.
Количество впрыскиваемого инжектором (форсункой) (21) топлива определяется сигналами, поступающими на бортовой компьютер, называемый электронным блоком управления (ЭБУ) (7). Топливо из бензобака (5) подается бензонасосом (3) и поступает далее через фильтр (4) во впускной трубопровод. Напряжение на бензонасос подается от замка зажигания через переключатель (1) и реле (2).
Топливо дозируется и впрыскивается во впускной трубопровод находящимися в нем форсунками (21), электрическая цепь которых соединена с ЭБУ. Таким образом, по сигналу ЭБУ изменяется количество топлива в камере сгорания двигателя.
Водитель управляет режимом работы двигателя, изменяя положение дроссельной заслонки (23), установленной перед впускным коллектором.
Для управления подачей воздуха при закрытой воздушной заслонке служит клапан холостого хода (18), включаемый ЭБУ по сигналу датчика положения дроссельной заслонки. Информация о количестве воздуха, поступающего в двигатель, и другие необходимые данные (положение коленчатого и распределительных валов, температура двигателя, детонация) поступают от соответствующих датчиков (16, 19, 20, 22, 24 и 25) в ЭБУ.
Важнейшим сигналом, обеспечивающим экологическую эффективность применения таких сравнительно дорогостоящих систем питания, является информация датчика кислорода. Этот датчик служит для косвенного определения и коррекции ЭБУ коэффициента избытка воздуха (l) в отработавших газах.
Устанавливаемый в выпускном тракте каталитический нейтрализатор (в обиходе катализатор) уменьшает сразу все основные компоненты вредных выбросов CO, CH, NOx, если выдерживается соотношение между топливом и воздухом для бензина 1:14,7; пропан‑бутана 1:16,1; компримированного природного газа 1:17,2. Эти соотношения соответствуют l=1. Кислородный датчик называют также лямбда‑зондом. Он постоянно определяет содержание неиспользованного в камере сгорания кислорода – косвенного показателя l. Эта информация позволяет ЭБУ путем изменения времени открытия форсунок (21) поддерживать l в узких пределах. Форсунка впрыскивает топливо в необходимых количествах для образования в камере сгорания смеси, для которой коэффициент l меньше единицы или близок к ней, и обеспечивает таким образом эффективную работу каталитического нейтрализатора.
Существует множество вариантов принципиальных и конструктивных схем впрысковых систем питания.
На рисунке 22 представлена схема распределенного или многоточечного впрыска. Существуют схемы центрального впрыска с одной или двумя форсунками на все цилиндры. Системы зажигания могут отличаться друг от друга, но все они управляются ЭБУ.
При переводе на газ впрысковых систем необходимо учитывать, что вмешательство в такие сложные системы может повлиять на их работоспособность и процесс подготовки смеси, начало подачи газа и его воспламенения. Если не учитывать этого, то при работе на газе могут возникнуть такие негативные явления, как хлопки в воздушном фильтре, впускном коллекторе двигателя, выход из строя бензиновых форсунок. Искрообразование происходит одновременно в двух цилиндрах двигателя, а также при большом угле одновременного открытия впускных и выпускных клапанов («перекрытие»). Из‑за перебоев в искрообразовании несгоревшая газовоздушная смесь воспламеняется на такте выпуска. При этом система может перестать работать на бензине.
Прежде чем приступить к переоборудованию топливной системы автомобиля, следует проконсультироваться о предстоящих работах с представителем завода‑изготовителя и, разумеется, совершенно необходимо хорошо знать бензиновую систему питания.
На впрысковые автомобили могут устанавливаться системы питания компримированного природного газа и газа сжиженного нефтяного.
Рассмотрим особенности перевода на газ на примере схемы распределенного впрыска.
Для работы на газовом топливе необходимо прежде всего отключить подачу бензина.
Существует два способа отключения подачи бензина.
Первый способ предусматривает полное отключение подачи топлива. Для этого в цепь управления штатным реле бензонасоса (3) устанавливают выключатель. Также в цепь управления форсунками (21) устанавливают реле выключения (8). Таким образом, при переключении на газ одновременно отключаются бензиновые инжекторы и топливный бензонасос.
Второй способ не предусматривает отключение бензонасоса, так как должно поддерживаться соответствующее давление бензина, чтобы без помех перейти с газа на бензин, а также избежать усыхания резинотехнических изделий системы питания. При этом сохраняется режим охлаждения инжекторов циркулирующим по основной и сливной магистралям топливом.
Для подачи газа используется газовая система питания, отличающаяся от устанавливаемых на карбюраторные автомобили тем, что в ней дополнительно установлены смеситель (17), дозатор (13) и согласующий электронный блок (12). В газовой системе могут устанавливаться блокировки подачи газа при запуске холодного двигателя и затрудненном запуске на газе.
Газовый смеситель (17) устанавливают между воздуховодом и корпусом дроссельной заслонки. Необходимое соотношение газовоздушной смеси обеспечивает дозатор газа (13). Это устройство оснащено шаговым электродвигателем, который по команде блока (12) изменяет проходное сечение трубки дозатора.
В ЭБУ заложена программа для работы на бензине, т. е. для обеспечения соотношения 1:14,7, и это необходимо учитывать при переоборудовании впрысковых автомобилей на газ. Для обеспечения коэффициента l>1 должны соблюдаться соотношения между воздухом и газом 1:16,1 (для пропан‑бутана) или 1:17,2 (для компримированного природного газа). Чтобы не выполнять дорогостоящего перепрограммирования, для работы на газе применяют дополнительные согласующие электронные блоки (12). В случае отключения форсунок бензина и ряда датчиков, вместо них подключают эмуляторы – электронные устройства, имитирующие работу бензиновых форсунок при переводе двигателя на газовое топливо (они «обманывают» ЭБУ, выдавая ему сигналы, что эти отключенные приборы работают нормально).
Опыт переоборудования инжекторных двигателей показывает, что для достижения цели достаточно отключить подачу бензина, установить смеситель и обычный дозатор газобензиновых систем. Однако такой кажущийся простым способ может привести к негативным последствиям. Так, при работе на газе инжекторных систем повышается вероятность обратного распространения пламени во впускной трубопровод, расходомер и воздушный фильтр из‑за внезапного обеднения смеси l>1 на переходных режимах. Возможны хлопки, которые могут разрушить корпус воздушного фильтра и повредить дорогостоящий расходомер воздуха, выполненный из платиновой проволоки толщиной 70 мкм. Для предотвращения этих явлений устанавливается дозатор, управляемый ЭБУ через согласующий блок. В корпусе воздушного фильтра устанавливают обратный предохранительный клапан («хлопушку») 1 – устройство, сбрасывающее излишнее давление во впускной трубе в момент хлопка газовоздушной смеси.
Установка остальных элементов газобаллонного оборудования аналогична переоборудованию карбюраторного автомобиля по традиционной схеме для газа.
Газобаллонные установки ЗАО «Автосистема»
Принципиальная схема оригинального газового оборудования, имеющего то же название, что и фирма‑изготовитель – «Автосистема», показана на рис. 23.
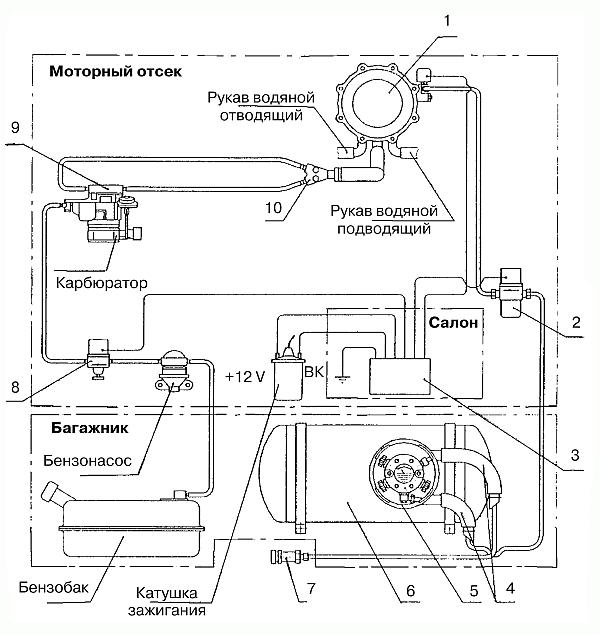
Рис. 23. Схема соединения и питания газовой аппаратуры «Автосистема»: 1 – редуктор‑испаритель; 2 – электромагнитный газовый клапан с фильтром; 3 – электронный блок управления; 4 – патрубки системы вентиляции блока запорно‑предохранительной арматуры; 5 – блок запорно‑предохранительной арматуры; 6 – баллон для ГСН; 7 – выносное заправочное устройство; 8 – электромагнитный бензиновый клапан; 9 – смеситель; 10 – тройник‑дозатор.
Сжиженный нефтяной газ хранится в газовом баллоне (6), рассчитанном на рабочее давление 1,6 МПа.
Баллон заправляют газом через выносное заправочное устройство (7) с установленным в нем обратным клапаном, предотвращающим выброс газа из баллона. Блок (5) запорно‑предохранительной арматуры включает в себя заправочный вентиль, предохранительный клапан, расходный вентиль жидкой фазы, устройство ограничения максимально допустимого уровня заправки газом. Система вентиляции состоит из прочного корпуса и прозрачной пластмассовой крышки, гибких вентиляционных шлангов (4) и двух фланцев. При закрытой крышке система полностью исключает попадание газа в салон автомобиля при нарушении герметичности элементов блока арматуры. Блок арматуры с системой вентиляции крепится к фланцу, расположенному на обечайке баллона.
От блока арматуры газ поступает по газопроводу в подкапотное пространство к электромагнитному газовому клапану‑фильтру (2) и затем по газопроводу к редуктору‑испарителю (1). Из редуктора через тройник‑дозатор (10) газ идет в смеситель (9). Для прерывания подачи бензина при работе на газовом топливе между бензонасосом и карбюратором установлен электромагнитный бензиновый клапан (8).
Для подогрева и испарения газа редуктор‑испаритель подключен шлангами к системе охлаждения двигателя.
Управление электромагнитными клапанами и другими электрическими элементами, являющимися составной частью ГБА, осуществляет электронный блок управления (3). Этот блок выпускают в нескольких модификациях, различающихся набором функций. Наиболее полная модификация имеет переключатели видов топлива, систему управления газовыми и бензиновыми клапанами в процессе пуска двигателя и систему управления углом опережения зажигания. При переходе с одного топлива на другое угол опережения зажигания автоматически меняется, при этом мощность искрового разряда при переходе на газ увеличивается на 35–40 %.
В блоке предусмотрена функция управления клапаном паровой фазы блока арматуры, что обеспечивает автоматическое включение и выключение клапана при достижении определенной температуры теплоносителя, обогревающего редуктор‑испаритель. Блок снабжен индикатором, показывающим уровень газа в баллоне.
Переход с бензина на газ и с газа на бензин осуществляет водитель со своего места без остановки автомобиля.
Особенности конструкции газовой аппаратуры «Автосистема»:
– унификация соединительных элементов по моделям автомобилей (легковые, грузовые и автобусы);
– взаимозаменяемость основных агрегатов на подобные других производителей;
– высокие эксплуатационные качества (устойчивый пуск холодного двигателя, простота обслуживания и ремонта);
– модульная компоновка основных агрегатов;
– выполнение резинотехнических изделий из материалов нового поколения, практически не требующих замены в течение 5–7 лет.
Одна из особенностей оборудования «Автосистемы» – это модульная компоновка. В стремлении более полно удовлетворить запросы автомобилистов, специалисты из множества вариантов блоков составляют нужную потребителю комплектацию. Однако этот подход имеет существенный недостаток – множится число регулировок: на редукторе два винта холостого хода, на экономайзере или дозаторе по два винта регулировки расхода топлива и т. д. Среднестатистический автомобилист не привык к такому обилию винтов. Обычно он обходится двумя винтами на карбюраторе. К тому же нельзя не отметить, что увеличение числа диафрагм и электроконтактов не повышает надежности системы.
Вариант схемы основных элементов ГБО, работающих на КПГ, представлен ЗАО «Автосистема» (рис. 24).
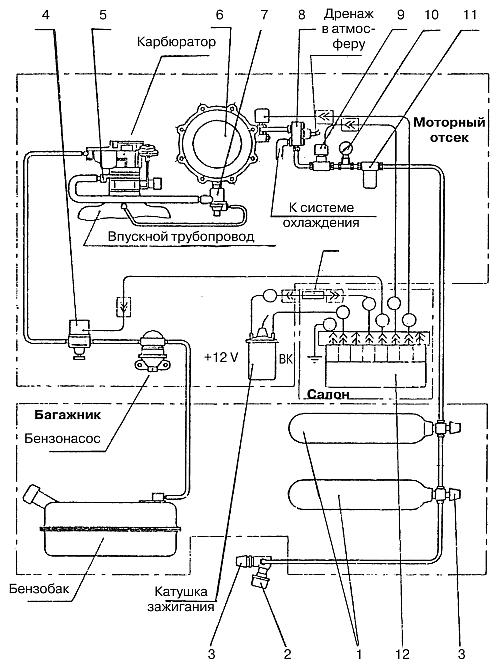
Рис. 24. Схема основных элементов ГБО, работающих на КПГ: 1 – баллоны газовые облегченные; 2 – узел заправочный выносной; 3 – вентиль; 4 – электромагнитный бензиновый клапан; 5 – смеситель газа; 6 – редуктор низкого давления; 7 – экономайзер; 8 – редуктор высокого давления; 9 – клапан электромагнитный газовый; 10 – манометр; 11 – газовый фильтр; 12 – электронный блок; 13 – предохранитель.
Компримированный природный газ (КПГ) хранится в двух баллонах (1), установленных в багажнике автомобиля. Они стянуты стальными хомутами и закреплены на кронштейнах. Баллоны поставляются в комплекте с вентилями.
Заправка баллонов КПГ производится на автомобильных газонаполнительных компрессорных станциях (АГНКС) под рабочим давлением 20 МПа.
Через выносной заправочный узел (2), вентили (3) газ поступает в баллоны по трубопроводам высокого давления. Затем он поступает к электромагнитному газовому клапану (9), рассчитанному на 20 МПа, предварительно пройдя очистку от твердых примесей в газовом фильтре (11). Манометр давления (10), установленный за газовым фильтром, осуществляет контроль наличия газа в баллонах. После открытия электромагнитного газового клапана газ подается к редуктору высокого давления (8), где давление газа снижается до 0,6–1,1 МПа. Затем по трубопроводу газ попадает в редуктор низкого давления (РНД) (6). При редуцировании (снижение давления) в редукторе высокого давления температура газа падает. К редуктору высокого давления по водяному рукаву подается теплоноситель от системы охлаждения двигателя. В РНД давление газа продолжает снижаться до величины, близкой к атмосферному давлению. РНД оборудован экономайзером (7), обеспечивающим обогащение газовоздушной смеси при полностью открытой дроссельной заслонке карбюратора.
По газовому рукаву газ поступает в смеситель (5), где он дозируется и смешивается с воздухом, после чего газовоздушная смесь подается в цилиндры двигателя. Чтобы перекрыть подачу бензина на время работы двигателя на газовом топливе, в бензопроводе между бензонасосом и карбюратором устанавливают электромагнитный бензиновый клапан.
Электромагнитными клапанами управляет электронный блок (12). Электрические схемы подключают к аккумуляторной батарее с помощью электропроводов через плавкий предохранитель (13), предназначенный для защиты всей системы от короткого замыкания и рассчитанный на ток в 3 А.
Автомобильные газовые топливные системы (АГТС) «САГА»
На базе научно‑производственной фирмы «САГА» и пермского агрегатного объединения «Инкар» создана аппаратура, позволяющая перевести на газовое топливо, сжиженное нефтяное (СНГ) или компримированное (метан), все классы автомобилей и автобусов, оснащенных карбюраторными, дизельными или впрысковыми двигателями внутреннего сгорания.
Эту аппаратуру можно устанавливать на легковые и грузовые автомобили, а также автобусы отечественного и иностранного производства.
Данная система позволяет формировать оптимальный состав газовоздушной смеси на всех режимах работы двигателя благодаря высокой точности редуцирования и регулирования давления газа на выходе из редуктора‑испарителя. Это обеспечивает стабильность работы двигателя, высокую топливную экономичность и снижение токсичности отработавших газов.
Конструктивные особенности системы и высокое качество ее изготовления в производственных условиях авиационного предприятия гарантируют высокую надежность, безопасность и простоту эксплуатации. Технический уровень системы соответствует международным требованиям ЕЭК ООН.
Все механические устройства указанного назначений, которые выпускались ранее, да и сейчас выпускаются многими фирмами, были сконструированы по карбюраторному принципу. Они включают в себя системы пуска, холостого хода, экономайзер, дозатор и предназначены, прежде всего, для установки на автомобилях с карбюраторными двигателями.
При разработке систем «САГА» учитывали, что главным параметром газа в отличие от бензина является давление. Поэтому была разработана конструкция редуктора‑испарителя с единой системой подачи топлива, не зависящей от остальных систем, которыми оснащен карбюратор. Редуктор поддерживает на выходе постоянное давление независимо от частоты вращения коленчатого вала двигателя и нагрузки.
Это оказалось вполне достаточно для устойчивой работы двигателя в любом режиме. Отсутствие дополнительных систем позволяет повысить надежность конструкции и устанавливать ее на карбюраторных и впрысковых двигателях.
Газобаллонное оборудование «САГА‑6»
Рассмотрим вариант газовой аппаратуры «САГА‑6» для работы на автомобиле с карбюраторным двигателем.
В комплект газовой аппаратуры «САГА‑6» входят редуктор‑испаритель (1) (рис. 25) и электромагнитные клапаны отключения газа (3) и бензина (8), отличающиеся от аналогичных элементов других систем повышенной надежностью, меньшим значением тока и напряжения срабатывания. Фильтры клапанов рассчитаны на длительный срок эксплуатации без какого‑либо обслуживания или замены.
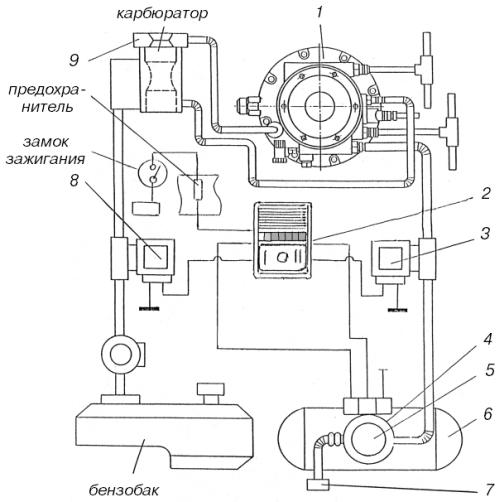
Рис. 25. Схема соединения газовой аппаратуры «САГА‑6»: 1 – редуктор‑испаритель; 2 – переключатель вида топлива и указатель уровня газа в баллоне; 3 – газовый электромагнитный клапан; 4 – газонепроницаемый кожух; 5 – блок запорно‑предохранительной арматуры; 6 – газовый баллон; 7 – выносная заправочная горловина; 8 – бензиновый электромагнитный клапан; 9 – газосмесительное устройство.
Трехпозиционным переключателем (2) (газ – нейтральное положение – бензин) при включенном зажигании выбирают необходимый вид топлива. Обычно переключатель встраивают в панель приборов автомобиля. Переключатель снабжен индикатором, который двумя светодиодами показывает выбранный вид топлива, а пятью светодиодами – уровень газа в баллоне. По мере расходования газа светодиоды по порядку, один за другим гаснут. Таким образом, водитель всегда может определить количество газа в баллоне.
Газовый баллон (6) с установленным на нем блоком запорно‑предохранительной арматуры (5) закрыт герметичным кожухом (4), который надежно изолирует оборудование от внутреннего объема автомобиля. В состав блока запорно‑предохранительной арматуры входит мультиклапан – ограничительный механизм, который отсекает подачу газа при заполнении баллона на 80 % от общего объема. Один из расходно‑наполнительных вентилей всегда находится в открытом положении. Заполняют баллон, не открывая крышку багажного отделения, через выносную заправочную горловину (7), обеспечивающую ускоренную (за 2–3 мин) заправку газом. Вентиль для соединения паровой фазы газа в баллоне с атмосферой позволяет заполнить баллон на 80 % даже при отсутствии компрессора на заправочной станции.
Смесительное устройство (9) (в обиходе просто смеситель) устанавливают над карбюратором в полости воздушного фильтра или между карбюратором и впускным трубопроводом. Смеситель вместе с редуктором‑испарителем 1 формируют оптимальный состав газовоздушной смеси. Форма и размеры смесителя подобраны так, чтобы он не влиял на показатели двигателя при его работе на бензине. Для разных марок карбюраторов и двигателей разработаны соответствующие модели смесителей.
В комплект оборудования входят также газопроводы, выполненные из нержавеющей стали, шланги из специальной резины и крепежные детали.
Система «САГА‑6» исключает попадание газа в салон автомобиля. Для этой цели конструкторы заменили традиционные резиновые кольца латунными, обеспечивающими герметичность на весь эксплуатационный период. В системе применены усовершенствованные диафрагмы редуктора‑испарителя, разработанные и произведенные совместно с фирмой EFFBE (Франция). Трубки газовой магистрали выполнены из нержавеющей стали с заводской развальцовкой. Соединительные элементы газовой магистрали выполнены по авиационной технологии. Предусмотрено надежное разгрузочное устройство с вакуумным управлением для предотвращения выхода газа в подкапотное пространство после остановки двигателя. При повреждении диафрагмы первой ступени редуктора‑испарителя газ также не поступает в подкапотное пространство. И, наконец, исключено попадание газа в систему охлаждения двигателя.
По конструкции аппаратура «САГА‑6» не повторяет ни одну из существующих зарубежных или отечественных систем. Она прошла испытание временем и завоевала признание.
Для автомобилей, оборудованных системами впрыска топлива, созданы разнообразные газосмесительные устройства, облегчающие их индивидуальный подбор для любой модели двигателя отечественного и иностранного производства.
Сочетание редуктора «САГА‑6» и специально подобранного смесителя (трубка Вентури) обеспечивает подачу газовоздушной смеси, состав которой близок к оптимальному на всех режимах работы двигателя.
«САГА‑6» легко поддается электронной коррекции и может работать с учетом сигналов лямбда‑зонда при установке на автомобиль каталитического нейтрализатора отработавших газов. При использовании системы «САГА» выбросы вредных веществ соответствуют не только требованиям Евро‑2, но и перспективным нормам Евро‑3.
Фирма «САГА» и ПО «Инкар» разработали комплектующие изделия и инструкцию по дооборудованию автомобильной газовой системы «САГА‑6» для применения на автомобилях с впрысковыми двигателями, в которой указаны порядок и способы выполнения операций по демонтажно‑монтажным и регулировочным работам при установке ГБО на конкретные автомобили.
Дооборудование автомобилей газовой топливной системой и получение российских сертификатов соответствия ГБО конкретным автомобилям следует проводить в соответствии с техническими условиями, установленными Министерством транспорта РФ‑ТУ 152‑12‑008‑99 «Переоборудование грузовых, легковых автомобилей и автобусов в газобаллонные для работы на сжиженных нефтяных газах. Приемка на переоборудование и выпуск после переоборудования. Испытание газобаллонных систем». Работы по переоборудованию следует выполнять только в специализированных мастерских.
Газобаллонное оборудование «САГА‑7»
Научно‑производственная фирма «САГА» и пермское авиационное объединение «ИНКАР» разработали, внедрили в производство и наладили выпуск автомобильной газовой топливной системы «САГА‑7» для использования компримированного природного газа – метана. Эту систему можно устанавливать на любые модели легковых автомобилей отечественного и иностранного производства (при рабочем объеме двигателя до 4,5 л). Она исключительно проста в эксплуатации, безопасна, высоконадежна и экономична.
В зависимости от марки автомобиля, конфигурации и массы баллонов на автомобиль устанавливают от одного до трех баллонов. На рис. 26 показана работающая на компримированном газе газобаллонная установка, содержащая три баллона (1) высокого давления. Каждый баллон представляет собой металлический корпус, покрытый армированным слоем стеклопластика, что повышает его прочность и уменьшает массу. Внутренняя поверхность баллонов имеет антикоррозионное покрытие. Баллоны крепятся с помощью кронштейнов и хомутов, предохраняющих их от перемещения и повреждений. Запас газа в трех баллонах рассчитан на пробег около 250 км.
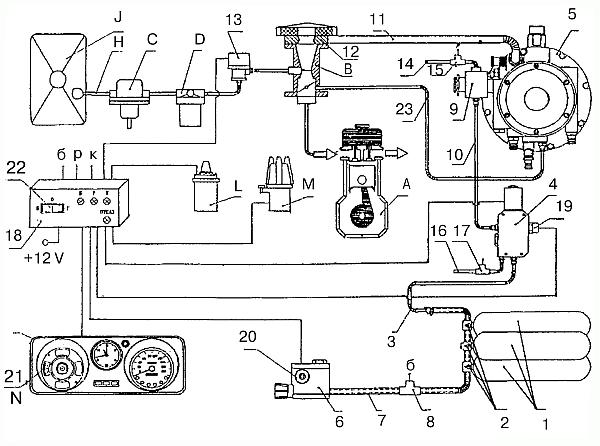
Рис. 26. Принципиальная схема автомобильной газовой топливной системы «САГА‑7».
Обозначение составных частей «САГА‑7»: 1 – баллоны; 2 – вентили баллонов; 3, 10 – трубопроводы высокого давления; 4 – газовый электромагнитный клапан; 5 – двухступенчатый редуктор‑подогреватель низкого давления; 6 – заправочное устройство; 7 – дренажный гофрированный шланг; 8, 15, 17 – датчики протечки газа (б – в багажном отделении, р – редукторе высокого давления, к – клапане газовом электромагнитном); 9 – редуктор высокого давления; 11 – трубопровод низкого давления; 12 – газовый смеситель; 13 – бензиновый электромагнитный клапан; 14 – дренажный шланг редуктора высокого давления; 16 – дренажный шланг газового электромагнитного клапана; 18 – электронное устройство; 19 – датчик давления газа; 20 – датчик блокировки запуска двигателя; 21 – указатель количества бензина в баке и давления (количества) газа в баллонах; 22 – трехпозиционный переключатель вида топлива «бензино‑газ»; 23 – вакуумный шланг.
Каждый баллон снабжен собственным вентилем (2), который содержит скоростной клапан и разрывную предохранительную мембрану (по температуре). Это предотвращает возможность разрыва баллона. Вентиль имеет дренажные каналы, по которым газ в случае утечки выводится через гибкие дренажные гофрированные шланги (7) за пределы автомобиля. В шланг вмонтирован датчик (8), сигнализирующий об утечке газа.
Баллоны заправляют одновременно через заправочное устройство (6), в котором также имеются дренажные каналы для отвода газа в случае его утечки. В корпусе заправочного устройства размещены фильтр, выдерживающий давление 20 МПа, заправочный вентиль и датчик блокировки пуска (20) двигателя в случае, если заправочный шланг АГНКС не отсоединен от заправочного устройства системы.
Баллоны соединены между собой трубопроводом высокого давления (3), переходящим в газовую магистраль. Трубопровод наружным диаметром 6 мм и внутренним 4 мм выполнен из нержавеющей стали с заводской развальцовкой и рассчитан на рабочее давление 20 МПа. Гайки и ниппели – «авиационной» конструкции.
На автомобиле установлен двухступенчатый редуктор‑подогреватель низкого давления (РНД) (5) из комплекта «САГА‑6», применяемый на газобаллонных автомобилях при использовании газа сжиженного нефтяного. Для работы двигателя на сжатом газе в него устанавливается выполненный с высокой точностью дополнительный узел‑редуктор высокого давления (РВД) (9), изготовленный из латуни. Он понижает давление с 20 до 0,5–1,2 МПа и обладает высокой надежностью и малыми размерами. Обогрев РВД осуществляется путем теплопередачи от РНД. Входной штуцер РВД снабжен фильтром, а на его корпусе размещен датчик (15), фиксирующий утечку газа, со штуцером для подключения дренажного гибкого шланга (14), по которому газ в случае утечки выводится за пределы автомобиля.
Шланг (11) соединяет выходной штуцер РНД с газовым смесителем (12), закрепленным на карбюраторе и предназначенным для приготовления газовоздушной смеси.
Газовая система питания также включает в себя электромагнитный газовый клапан (ЭМК) 4, рассчитанный на давление 29 МПа, фильтр, датчик (17), определяющий утечку газа, со штуцером для подключения гибкого дренажного шланга (16), датчик давления (количества газа (19), показывающий на приборном щитке автомобиля К количество оставшегося газа в баллонах.
Бензиновая система питания при установке систем для использования КПГ содержит традиционные элементы: карбюратор, бензиновый электромагнитный клапан (13), фильтр тонкой очистки (D), бензонасос (C), бензопровод (H) и бензобак (J).
Штатный указатель (21) уровня бензина при работе на этом топливе показывает его количество в бензобаке, а при работе на газе – количество (давление) газа в баллонах.
Газобаллонную установку рассматриваемой конструкции отличает от других наличие электронного устройства (18), включающего в себя корректор угла опережения зажигания. Оно позволяет мгновенно переходить с бензина на газ и подстраиваться под частоту вращения коленчатого вала. При низкой частоте вращения коленчатого вала электрическое устройство увеличивает угол опережения зажигания для газа, при высокой частоте – снижает по сравнению с работой двигателя на бензине.
Автоматическое электронное устройство (18), представляющее собой блок обработки сигналов, поступающих от датчиков импульсов, обеспечивает:
– звуковую и световую сигнализацию в салоне водителя об утечке газа и о том, где именно произошла утечка: в багажном отделении, редукторе высокого давления, или в электромагнитном газовом клапане;
– согласование датчика давления газа в баллонах с указателем уровня бензина в комбинации приборов автомобиля;
– выключение электромагнитного газового клапана при остановке двигателя;
– блокировку пуска двигателя, если заправочный шланг газонаполнительной станции не отключен от заправочного устройства системы;
– переключение на другой вид топлива;
– автоматический встроенный контроль исправности электронного устройства.
При работе газобаллонной установки компримированный (сжатый) природный газ из баллонов (1) высокого давления через вентили (2) попадает в трубопровод высокого давления (3), а затем в электромагнитный клапан (4) с фильтром. Здесь газ очищается от механических примесей и поступает в прогретый теплоносителем редуктор высокого давления (9), где давление газа понижается до 0,5–1,2 МПа. Далее вся работа газобаллонной установки идет по традиционной схеме, как и для сжиженного газа.
Date: 2015-07-17; view: 1134; Нарушение авторских прав Понравилась страница? Лайкни для друзей: |
|
|