Главная
Случайная страница
Полезное:
Как сделать разговор полезным и приятным
Как сделать объемную звезду своими руками
Как сделать то, что делать не хочется?
Как сделать погремушку
Как сделать так чтобы женщины сами знакомились с вами
Как сделать идею коммерческой
Как сделать хорошую растяжку ног?
Как сделать наш разум здоровым?
Как сделать, чтобы люди обманывали меньше
Вопрос 4. Как сделать так, чтобы вас уважали и ценили?
Как сделать лучше себе и другим людям
Как сделать свидание интересным?
Категории:
АрхитектураАстрономияБиологияГеографияГеологияИнформатикаИскусствоИсторияКулинарияКультураМаркетингМатематикаМедицинаМенеджментОхрана трудаПравоПроизводствоПсихологияРелигияСоциологияСпортТехникаФизикаФилософияХимияЭкологияЭкономикаЭлектроника
|
Руководитель курсового проекта _____
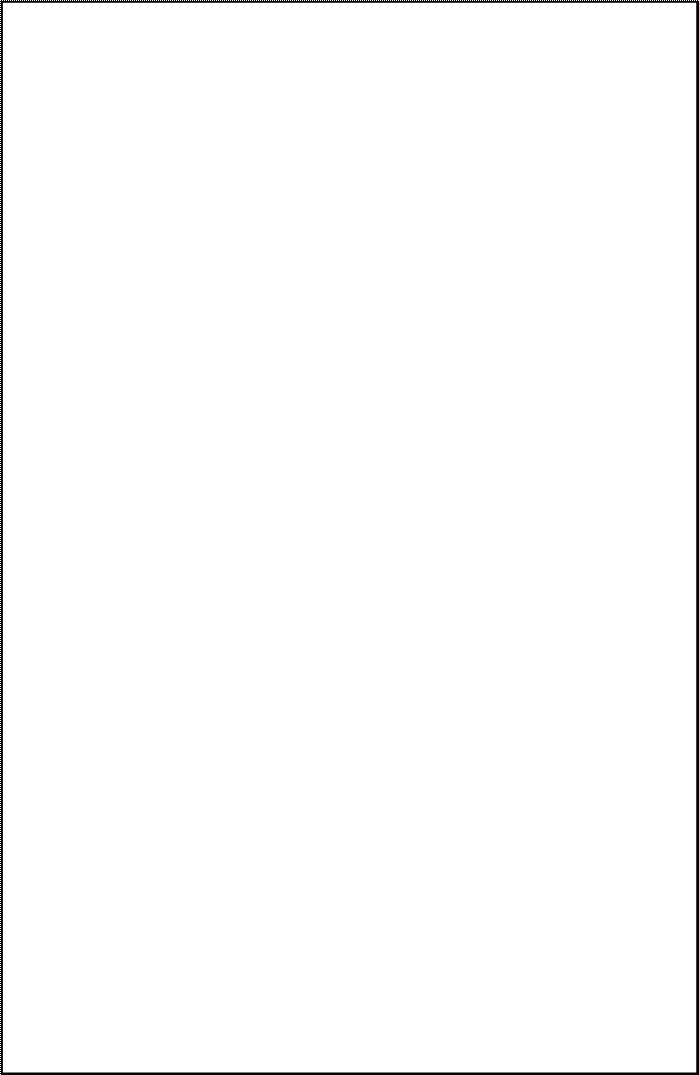
А2. Титульный лист курсового проекта
Министерство образования Республики Беларусь
Минский государственный автомеханический колледж
2 – 37 01 06 "Техническая эксплуатация автомобилей"
Группа ________
КУРСОВОЙ ПРОЕКТ
Ремонт автомобилей
Разработка технологического процесса
восстановления детали № …………………
«……………………………………………………..»
ПОЯСНИТЕЛЬНАЯ ЗАПИСКА
Разработал ___________ ________ И.О.Фамилия
подпись дата
Консультант ___________ _______ И.О.Фамилия
подпись дата
200_
А3. Содержание пояснительной записки
Содержание
Введениe.............................................................................................................…………..
1 Общая часть...................................................................................................…….…….
1.1 Хаpактеpистика детали..................................................................................…
1.2 Технические тpебования на дефектацию детали..............................…..........
1.3 Дефекты детали и пpичины их возникновения..................................…........
1.4 Технические тpебования к отpемонтиpованной детали......................….......
1.5 Выбоp pазмеpа паpтии деталей....................................................................….
2 Технологическая часть................................................................................….….........
2.1 Маpшpут pемонта.......................................................................................…...
2.2 Выбоp pационального способа восстановления детали........................….....
2.3 Выбоp технологических баз.......................................................................…..
2.4 Технологические схемы устpанения дефектов………........................…........
2.5 Расчет пpипусков.........................................................................................…..
2.6 Технологический маpшpут восстановления детали............................…........
2.7 Выбоp обоpудования и технологической оснастки........................................
2.8 Расчет pежимов обpаботки.........................................................................…..
2.9 Расчет ноpм вpемени..................................................................................……
2.10 Требования безопасности при выполнении восстановительных
работ…………………………………………………………………………..
2.11 Технологическая документация……………………………………………..
2.12 Расчет годового объема работ……………………………………………….
2.13 Расчет годовых фондов времени…………………………………………….
2.14Расчёт числа основных рабочих…………………………………………….
2.15 Организация технологического процесса на участке………………………
2.16 Расчёт количества технологического, подъемно-транспортного оборудования и выбор организационной оснастки……………………………………
2.17 Расчёт площади участка………………………………………………………
2.18 Проектирование планировки участка восстановления…………………….
3 Констpуктоpская часть...............................................................................……………
3.1 Анализ существующих конструкций приспособления……………………….
3.2 Назначение и устpойство приспособления...……………………..........…......
3.3 Принцип действия приспособления…………………………………………..
3.4 Расчет пpиспособления...............................................................................……
3.5 Обоснование конструкции приспособления…………………………………
Заключение.........................................................................................................………….
Список использованных источников..........................................................…..……….
Пpиложение А (Ремонтный чертеж)..............................................................…….……..
Приложение Б (Комплект технологических документов)..………..……………………
Приложение В (Спецификации)………………………………………..…………………
Приложение Б
Таблица Б1 Стандарты на материалы и сплавы [14]
Материалы и сплавы
| Номер стандарта
| Серый чугун
| ГОСТ 1412-85
| Ковкий чугун
| ГОСТ 1215-79
| Высокопрочный чугун
| ГОСТ 7293-85
| Антифрикционный чугун
| ГОСТ 1585-85
| Сталь углеродистая обыкновенная
| ГОСТ 380-94
| Сталь углеродистая качественная конструкционная
| ГОСТ 1050-88
| Сталь углеродистая инструментальная
| ГОСТ 1435-90
| Сталь легированная конструкционная
| ГОСТ 4543-71 до1.01.1995
| Алюминиевые сплавы (литейные)
| ГОСТ 1583-93
| Латунь (ленты)
| ГОСТ 2208-91
| Латунь (листы и полосы)
| ГОСТ 931-90
| Бронзы безоловяные литейные
| ГОСТ 493-79
| Бронзы безоловяные деформируемые
| ГОСТ 18175-78
| Таблица Б2 Перевод чисел твердости HRC в числа твердости HRCэ (выборочно)[15]
HRC
| HRCэ
| HRC
| HRCэ
| HRC
| HRCэ
| 19,9
20,0
21,9
23,0
24,0
25,0
26,0
27,1
28,1
29,1
30,2
31,2
32,2
33,2
| 22,0
23,0
24,0
25,0
26,0
27,0
28,0
29,0
30,0
31,0
32,0
33,0
34,0
35,0
| 34,4
35,3
36,3
37,4
38,4
39,4
40,5
41,5
42,5
43,5
44,6
45,6
46,6
47,7
| 36,0
37,0
38,0
39,0
40,0
41,0
42,0
43,0
44,0
45,0
46,0
47,0
48,0
49,0
| 48,7
49,7
50,7
51,8
52,8
53,8
54,9
55,9
56,9
58,0
59,0
60,0
61,0
62,1
| 50,0
51,0
52,0
53,0
54,0
55,0
56,0
57,0
58,0
59,0
60,0
61,0
62,0
63,0
| Примечание: Промежуточные значения находятся методом линейной интерполяции.
Приложение В
Таблица В1 Классы и параметры шероховатости поверхности по ГОСТ2789-73
Класс
шероховатости
| Параметр шероховатости, мкм
| Ra
| Rz
|
-
|
[100]
|
[400]
|
|
[50]
|
[200]
|
|
[25]
|
[100]
|
| 20,0
16,0
[12,5]
|
[50]
|
| 10,0
8,0
[6,3]
|
[25]
|
| 5,0
4,0
[3,2]
|
[12,5]
|
| 2,5
2,0
[1,6]
| 10,0
8,0
[6,3]
|
| 1,25
1,00
[0,80]
| 5,0
4,0
[3,2]
|
| 0,63
0,50
[0,40]
| 2,5
2,0
[1,6]
|
| 0,35
0,25
[0,20]
| 1,25
1,00
[0,80]
|
| 0,160
0,125
[0,100]
| 0,63
0,50
[0,40]
|
| 0,080
0,063
[0,050]
| 0,32
0,25
[0,20]
|
| 0,040
0,032
[0,025]
| 0,160
0,125
[0,100]
|
| 0,020
0,016
[0,012]
| 0,080
0,063
[0,050]
|
| 0,010
0,008
[0,001]
| 0,040
0,032
[0,025]
| Примечание: [ ] - предпочтительное значение.
Таблица В2 Средняя точность обработки и параметры шероховатости обработанной
поверхности при обработке наружных поверхностей тел вращения
Способ обработки
| Квалитет
| Параметр
шероховатости Ra, мкм
| Обтачивание однократное
|
| 6,3
| Обтачивание предварительное
Обтачивание чистовое
| 11…10
| 3,2
| Обтачивание однократное
Шлифование однократное
| 10…8
| 1,6…0,8
| Обтачивание предварительное
Обтачивание чистовое
Шлифование однократное
|
8…6
|
0,8
| Обтачивание предварительное
Обтачивание чистовое
Обтачивание тонкое
|
7…6
|
0,4
| Обтачивание однократное
Шлифование предварительное
Шлифование чистовое
|
7…6
|
0,4
| Обтачивание предварительное
Обтачивание чистовое
Шлифование предварительное
Шлифование чистовое
|
|
0,4
| Обтачивание предварительное
Обтачивание чистовое
Шлифование предварительное
Шлифование тонкое
|
6…5
|
0,2
| Обтачивание предварительное
Обтачивание чистовое
Шлифование чистовое
Шлифование тонкое
|
|
0,2…0,1
|
Таблица В3 Средняя точность и параметры шероховатости отработанной поверхности цилиндрических отверстий
Способ обработки
| Квалитет
| Параметр шероховатости Ra, мкм
| В сплошном металле
Сверление 12 25…12,5
Сверление и зенкерование 11 6,3…3,2
Сверление и развертывание 8…9 3,2…1,6
Сверление и протягивание 9…8 3,2…0,4
Сверление, зенкерование и развертывание 9…8 1,6…0,8
Сверление и двукратное развертывание 8…7 1,6…0,4
Сверление, зенкерование и двукратное развертывание 8…7 0,8…0,4
Сверление, зенкерование и шлифование 8…7 0,8…0,4
Сверление, протягивание и калибрование 8…7 0,8…0,4
| В заготовках с отверстиями
Зенкерование или растачивание 12 6,3…3,2
Рассверливание 12 25…6,3
Двукратное зенкерование или двукратное растачивание 11 12,5…6,3
Зенкерование или растачивание и развертывание 9…8 3,2…1,6
Зенкерование и растачивание 9…8 6,3…3,2
Двукратное зенкерование и развертывание или
двукратное растачивание и развертывание 9…8 1,6…0,8
Зенкерование или растачивание и двукратное развертывание 8…7 0,8…0,4
Зенкерование или двукратное растачивание и
двукратное развертывание или тонкое растачивание 8…7 0,8…0,4
Зенкерование или двукратное растачивание и хонингование 8…7 0,2…0,05
Зенкерование и растачивание, тонкое растачивание и
хонингование 8…7 0,1…0,025
Протягивание и шлифование 8…7 0,8…0,2
| Таблица В4 Средняя точность и параметры шероховатости обработанных плоскостей
поверхностей
Способ обработки
| Квалитет
| Параметр шероховатости
Ra, мкм
| Строгание и фрезерование цилиндрическими и
торцовыми фрезами:
черновое 14…11 12,5…3,2
получистовое и однократное 12…11 3,2…1,6
чистовое 10 1,6…0,8
тонкое 8…10 1,6…0,2
Протягивание:
черновое литых и штампованных поверхностей 11…10 3,2…1,6
чистовое 8…6 1,6…0,4
Шлифование:
однократное 8…7 1,6…0,4
предварительное 9…8 0,8…0,4
чистовое 7 0,4…0,1
тонкое 6 0,2…0,05
|
Примечание:
1. Данные относятся к обработке жестких деталей с габаритными размерами не более 1м при базировании по чисто обработанной поверхности и использовании ее в качестве измерительной базы.
2. Точность обработки торцевыми фрезами при сопоставимых условиях выше, чем цилиндрическими, примерно на один квалитет.
3. Тонкое фрезерование производят только торцовыми фрезами.
Таблица В5 Средняя точность и параметры шероховатости обработанных резьбовых
поверхностей
Способ обработки
| Квалитет
| Параметр шероховатости
Ra, мкм
| Круглыми плашками 8g 12,5…6,3
Метчиком 6H 6,3…3,2
Фрезерование:
дисковыми фрезами 6g 6,3…1,6
гребенчатыми резцами 6g 6,3…3,2
Точение:
резцами 4h 3,2…0,8
гребенками 6g 6,3…0,8
вращающимися резцами (вихревой метод) 6h 3,2…1,6
самораскрывающимися головками 4h 6,3…1,6
Накатывание:
плоскими плашками 6g 0,8…0,4
резьбонакатными роликами 4h…4g 0,8…0,2
|
Таблица В6 Рекомендуемая замена резьбы [9]
Болты
| Гайки
| Поле допуска по ранее
действующему
ГОСТ 9253-59
| Поле допуска по
ГОСТ 16093-2004
| Поле допуска по ранее
действующему
ГОСТ 9253-59
| Поле допуска по
ГОСТ 16093-2004
| Кл. 1
Кл. 2
Кл. 2а
Кл. 3
| 4h
6d
6d
8d
| Кл. 1
Кл. 2
Кл. 2а
Кл. 3
| 4H, 5H
6H
6H
7H
|
Таблица В7 Средняя точность обработки зубчатых колес
Способ обработки
| Квалитет
| Параметр шероховатости
Ra, мкм
| Фрезерование:
предварительное 9…10 12,5…3,2
окончательное дисковой фрезой 8…9 6,3…1,6
окончательное червячной фрезой 7…8 6,3…1,6
Долбление чистовое 6…8 3,2…0,8
Протягивание 6…7 3,2…0,8
Строгание чистовое 5…7 3,2…0,8
Хонингование 6…7 1,6…0,4
Шлифование 4…5 0,8…0,2
|
Таблица В8 Экономически достижимая размерная точность изготовления деталей из стали
при различных методах обработки
Вид
поверхности
| Метод обработки
| Класс точности
по ОСТ
| Квалитет
|
Вал
| Обтачивание на станках:
автоматах
револьверных
токарных
Обтачивание алмазное
Шлифование:
бесцентровое
в центрах
тонкое
Обкатывание роликом или шариком
Электроэрозионная обработка
Суперфиниширование
Доводка (ручная или механическая)
|
3а, 3
3, 2а
2а, (2)
2, (1)
2, 1
1, выше 1-го
3, 2
5…2
1, выше 1-го
1, выше 1-го
|
10, 8
8, 7
7, (6)
6, (5)
6, 5
8, 6
13…6
|
Отверстие
| Сверление:
ручное
через кондуктор
после предварительного сверления
Зенкерование
Растачивание на станках
автоматах
револьверных
токарных
координатно-расточных
Растачивание алмазное
Развертывание:
однократное
многократное
Протягивание
Прошивание
Развальцовывание
Раскатывание
Калибрование
Шлифование
Хонингование
Суперфиниширование
Доводка (ручная или механическая)
Электроэрозионное прошивание
Электрохимическое:
прошивание
хонингование
Электроалмазное шлифование
|
5, (4)
4, (3а)
4, (3а)
4, 3а
3, 3а
2а, 3
2а, (2)
2, (1)
2, (1)
2а
2, (1)
2, (1)
2, 1
2, 1
3, 2
2, (1)
2, 1 (выше 1-го)
2, 1
1, выше 1-го
1, выше 1-го
5…2
5…2
2, 1
2, 1
|
13, (11)
11, (10)
11, (10)
11, (10)
8…10
7…9
7, (6)
6, (5)
6, (5)
6, (5)
6, (5)
6, 5
6, 5
8…6
6, (5)
6, 5
13…6
13…6
6, 5
6, 5
|
Плоскость
| Строгание
Долбление
Фрезерование
Обтачивание торцов на станках:
автоматах
револьверных
токарных
Шлифование:
торцов
плоскостей
Хонингование
Суперфиниширование
Доводка (ручная или механическая)
Шабрение
Слесарная опиловка
| 3а, 3
5, (4)
3, 2а, (2)
3, (2а)
2а, 2
2, (1)
2, (1)
1, выше 1-го
1, выше 1-го
3, 2а, (2)
4, 3а, (3)
| 10, 8
12, 11
8…6
8, (7)
7, 6
6, (5)
6, (5)
8…6
11, 10, (8)
|
Резьба
| Нарезание:
плашкой-метчиком
резцом-гребенкой
фрезой
Накатывание роликами
Шлифование
|
3, 2
3, 2, (1)
3, 2а, (2)
2, 1
|
8…6
8…6, (5)
8, 7, (6)
6, (5)
| Контурные
поверхности
плоских
деталей
| Холодная штамповка:
вырубка
пробивка
зачистка
зачистка с калибровкой
|
|
| Полая деталь
простой
формы
| Холодная штамповка в вытяжных штампах:
по диаметру
по высоте
|
4, 3а
5…3
|
11, 10
12…9
|
Примечание: 1. Более высокие квалитеты относятся к тем случаям, когда детали изготовляют небольшими партиями на станках высокой точности.
2. Классы точности и квалитеты, указанные в скобках, относятся в основном не к экономически, а технологически достижимым.
Таблица В9 Шероховатость поверхности после различных видов и методов обработки стали
Вид и метод обработки
|
Ra, мкм
|
Rz, мкм
| Класс шероховатости
по ГОСТ 2789-73
|
Обработка наружных цилиндрических поверхностей
Отрезка:
резцом 80…25 320…60 1…3
фрезой 50…25 180…90 1…3
абразивная 6,3…3,2 30…15 4…5
приводной пилой 50…25 180…90 1…3
Подрезание торцов 1,25…3,2 50…15 3…5
Обтачивание:
черновое 40…20 160…80 2…3
получистовое 20…5,0 80…20 3…5
чистовое 10…1,25 40…6,3 4…7
тонкое (алмазное) 1,25…0,32 6,3…1,6 7…9
Нарезание резьбы:
плашкой 10…5,0 40…20 4…5
резцом, фрезой 5,0…1,25 20…6,3 5…7
вращающимися резцами 6,0…0,8 30…4,0 4…7
накатывание роликами 1,25…0,63 6,3…3,2 7…8
Шлифование:
предварительное 2,5…1,25 10…6,3 6…7
чистое 1,25…0,63 6,3…3,2 7…8
тонкое 0,63…0,16 3,2…0,8 8…10
электроалмазное 0,32…0,08 1,6…0,4 9…10
электроэрозионное 1,25…0,32 6,3…0,4 7…9
Обкатывание роликами и шариками 1,25…0,08 6,3…0,4 7…11
Алмазное выглаживание 1,25…0,04 6,3…0,2 7…12
Суперфиниширование:
чистовое 0,16…0,08 0,8…0,4 10…11
отделочное 0,04…0,01 0,2…0,05 12…14
Притирка, доводка, 0,08…0,01 0,4…0,05 11…14
Полирование пастой 0,32…0,02 1,6…0,10 9…13
|
Обработка внутренних цилиндрических поверхностей
Сверление:
до 15 мм 12,5…5,0 50…20 3…5
св. 15 мм 25…12,5 90…50 2…3
Рассверливание 25…6,3 90…20 2…4
Зенкерование:
черновое (по корке) 25…12,5 90…50 2…3
чистовое 6,3…3,2 20…15 4…5
Развертывание:
предварительное 2,5…1,25 10…6,3 6…7
окончательное 1,25…0,32 6,3…1,6 7…9
Нарезание резьбы:
метчиками 10…5,0 40…20 4…5
резцом, гребенкой 5,0…1,25 20…6,3 5…7
фрезой 5,0…1,6 20…8 5…6
Протягивание:
чистовое 1,25…0,63 6,3…3,2 7…9
отделочное 0,63…0,16 3,2…0,8 8…10
Растачивание:
черновое 80…50 320…180 1
получистовое 25…12,5 90…50 2…3
чистовое 5,0…2,5 20…10 5…6
тонкое алмазное 1,25…0,32 6,3…1,6 7…9
Шлифование:
получистовое 6,3…3,2 30…15 4…5
чистовое 1,25…0,63 6,3…3,2 7…8
тонкое 0,63…0,16 3,2…0,8 8…10
электроалмазное 0,32…0,08 1,6…0,4 9…11
Хонингование:
чистое 0,63…0,32 3,2…1,6 8…9
отделочное 0,16…0,01 0,8…0,1 10…13
электрохимическое 0,08…0,01 0,4…0,1 11…14
Раскатывание, калибрование,
алмазное выглаживание 0,63…0,08 3,2…0,4 8…11
Прошивание:
электроэрозионное 20…0,32 80…16 3…9
электрохимическое 0,32…0,16 1,6…0,8 9…10
ультразвуком 0,63…0,16 3,2…0,8 8…10
электронным лучом 1,25…0,16 6,3…0,8 7…10
Полирование пастой 0,63…0,08 3,2…0,4 8…11
Притирка, доводка 0,16…0,01 0,8…0,05 10…14
|
Обработка плоских поверхностей
Строгание:
черновое 25…12,5 90…50 2…3
чистовое 6,3…3,2 30…15 4…5
Фрезерование цилиндрической фрезой:
черновое 50…25 170…90 1…2
чистовое 6,3…3,2 30…15 4…5
тонкое 1,6 8 6
Фрезерование торцовой фрезой:
черновое 12,5…6,3 50…30 3…4
чистовое 6,3…3,2 30…15 4…5
тонкое 1,6…0,63 8…3,2 6…8
Протягивание 5,0…1,25 20…6,3 5…7
Шлифование:
получистовое 3,2 15 5
чистовое 1,25…0,63 6,3…3,2 7…8
тонкое 0,63…0,16 3,2…0,8 8…10
Шабрение:
обычное 2,5…0,63 10…3,2 6…8
тонкое 0,63…0,16 3,2…0,8 8…10
Полирование:
пастой 0,63…0,04 3,2…0,2 8…12
электрохимическое 0,04…0,01 0,2…0,06 12…14
Притирка 3,2…0,1 15…0,5 5…10
Доводка:
грубая 0,4 1,8 8
средняя 0,2…0,1 0,9…0,5 9…10
тонкая 0,05 0,2 12
отделочная (зеркальная) 0,025…0,01 0,10…0,025 14
|
Приложение Г
Таблица Г1 Минимальные припуски на механическую обработку после нанесения
покрытия [23]
Способ нанесения покрытия
| Припуск на диаметр, мм
| Ручная наплавка
Наплавка под слоем флюса
Вибродуговая наплавка
Железнение
Хромирование
Напыление
| 4…6
1,6…2
0,4…1,0
0,1…0,3
0,5…1
|
Таблица Г2 Припуски на обработку наружных поверхностей [23, 25]
Вид обработки вала
| Длина вала,
мм
| Припуск на диаметр для интервала диаметров (свыше – до), мм
| 10…18
| 18…30
| 30…50
| 50…80
| 80…120
| 120…180
| Черновое точение с
установкой в
патроне и центрах:
отливки:
из серого чугуна
из ковкого чугуна
из бронзы
горячештампованной
заготовки
кованой поковки
холодноштампованной
заготовки
|
l / d ≤ 10
|
-
2,0
-
1,2
2,0
1,5
|
-
2,0
2,5
1,5
2,0
1,5
|
3,0
2,5
2,5
1,6
2,5
2,0
|
3,5
3,0
3,0
2,5
3,0
2,0
|
4,0
3,0
3,5
2,5
3,0
2,5
|
5,0
4,0
4,5
4,0
5,0
4,0
| Чистовое точение
после чернового
| От 90 до 300
300…500
500…800
| 1,0
1,2
-
| 1,2
1,3
1,4
| 1,2
1,4
1,5
| 1,4
1,5
1,6
| 1,5
1,6
1,7
| 1,7
1,8
1,9
| Шлифование после
чистового обтачивания
| До 100
100…200
200…400
400…700
| 0,25
0,30
-
-
| 0,30
0,35
0,40
-
| 0,30
0,35
0,40
0,45
| 0,35
0,40
0,45
0,55
| 0,45
0,50
0,55
0,60
| 0,50
0,55
0,60
0,65
| Шлифование после
чистового обтачивания
закаленных заготовок
| От 90 до 100
100…300
300…600
600…1000
| 0,30
0,35
-
-
| 0,35
0,40
0,45
-
| 0,40
0,50
0,55
0,70
| 0,45
0,55
0,65
0,75
| 0,55
0,60
0,70
0,80
| 0,6
0,7
0,8
-
| Примечание. Припуски на черновую обработку приведены без учета дефектного слоя детали.
Таблица Г3 Припуски на тонкое (алмазное) обтачивание валов [25]
Материал заготовки
| Диаметр обрабатываемой
детали, мм
| Припуск на диаметр, мм
| Легкие сплавы
| До 100
Св. 100
| 0,3
0,5
| Бронза и чугун
| 0,3
0,4
| Сталь
| 0,2
0,3
| Примечание. В случае применения двух резцов (чернового и чистового) на чистовую обработку оставляют припуск 0,1 мм.
Таблица Г4 Припуски на чистовое обтачивание валов [25]
Диаметр вала
(свыше - до), мм
| Припуск на диаметр (мм) при длине обрабатываемого вала (свыше - до), мм
| До 100
| 100…250
| 250…500
| 500…800
| 800…1200
| 1200…2000
| До 10
10…18
18…30
30…50
50…80
80…120
| 0,8
0,9
0,9
1,0
1,1
1,1
| 0,9
0,9
1,0
1,0
1,1
1,2
| 1,0
1,0
1,1
1,1
1,2
1,2
| -
1,1
1,3
1,3
1,4
1,4
| -
-
1,4
1,5
1,6
1,6
| -
-
-
1,7
1,8
1,9
| Примечание:
- Для мелкосерийного производства припуск определяют умножением табличной величины на коэффициент 1,3 с округлением до десятых долей в сторону увеличения. Допуск на предварительную обработку назначают по 14-му квалитету.
- Поле допуска диаметров валов – h12.
Таблица Г5 Припуски на шлифование валов [25]
Диаметр
вала
(св. - до), мм
| Вид
шлифования
| Состояние
материала
| Припуск на диаметр (мм) при длине вала (свыше – до), мм
| До 100
| 100…250
| 250…500
| 500…800
| 800…1200
| До 10
| Центровое
| Сырой
| 0,2
| 0,2
| 0,3
| 0,4
| -
| Закаленный
| 0,3
| 0,3
| 0,4
| 0,5
| -
| Бесцентровое
| Сырой
| 0,2
| 0,2
| 0,2
| 0,3
| -
| Закаленный
| 0,3
| 0,3
| 0,4
| 0,5
| -
| 10…18
| Центровое
| Сырой
| 0,2
| 0,3
| 0,3
| 0,3
| 0,4
| Закаленный
| 0,3
| 0,3
| 0,4
| 0,5
| 0,6
| Бесцентровое
| Сырой
| 0,2
| 0,2
| 0,2
| 0,3
| 0,4
| Закаленный
| 0,3
| 0,3
| 0,4
| 0,5
| 0,5
| 18…30
| Центровое
| Сырой
| 0,0
| 0,3
| 0,3
| 0,4
| 0,4
| Закаленный
| 0,3
| 0,4
| 0,4
| 0,5
| 0,6
| Бесцентровое
| Сырой
| 0,3
| 0,3
| 0,3
| 0,3
| 0,4
| Закаленный
| 0,3
| 0,4
| 0,4
| 0,5
| 0,6
| 30…50
| Центровое
| Сырой
| 0,3
| 0,3
| 0,4
| 0,5
| 0,6
| Закаленный
| 0,4
| 0,4
| 0,5
| 0,6
| 0,7
| Бесцентровое
| Сырой
| 0,3
| 0,3
| 0,3
| 0,4
| 0,5
| Закаленный
| 0,4
| 0,4
| 0,5
| 0,5
| 0,6
| 50…80
| Центровое
| Сырой
| 0,3
| 0,4
| 0,4
| 0,5
| 0,6
| Закаленный
| 0,4
| 0,5
| 0,5
| 0,6
| 0,8
| Бесцентровое
| Сырой
| 0,3
| 0.3
| 0,3
| 0,4
| -
| Закаленный
| 0,4
| 0,5
| 0,5
| 0,6
| -
| Примечание:
- Для мелкосерийного или единичного производства величина припуска определяется умножением табличной величины на коэффициент 1,2.
- Поле допуска диаметров валов - h11.
Таблица Г6 Припуски для снятия цементированного слоя [25]
Глубина
цементированного слоя
(свыше – до), мм
| Интервалы размеров (свыше – до), мм
| Поверхности
| Цилиндрические
наружные и внутренние
| Плоские
(в том числе торцовые)
| Припуск, мм
| на диаметр
| на сторону
| 0,46…0,6
| До 30
| 1,5
| 1,0
| 30…50
| 1,7
| 50…80
| 80…120
| 1,2
| 120…180
| 0,6…0,8
| До 30
| 2,0
| 30…50
| 2,2
| 50…80
| 80…120
| 120…180
| 180…260
| 1,5
| 0,8…1,1
| До 30
| 2,5
| 30…50
| 2,7
| 1,7
| 50…80
| 80…120
| 120…180
| 3,0
| 2,0
| 180…260
| 260…360
| 360…500
| 1,1…1,4
| До 30
| 3,2
| 1,8
| 30…50
| 3,5
| 2,0
| 50…80
| 80…120
| 120…180
| 4,0
| 2,3
| 180…260
| 260…360
| 360…500
|
Таблица Г7 Припуски при протягивании отверстий [25]
Размеры протягиваемого
отверстия, мм
| Припуск на диаметр, мм
| Размеры протягиваемого
отверстия, мм
| Припуск на диаметр, мм
| Длина
| Диаметр
| Длина
| Диаметр
| 6…50
6…120
11…180
30…180
| от 10 до 18
18…30
30…50
50…80
| 0,2…0,5
0,3…0,6
0,4…0,7
0,6…0,8
| 4…3
3…2,5
2,5…1,5
1,5…1,0
| 80…120
120…180
180…260
260…360
| 1,0
1,2
1,4
1,6
|
Таблица Г8 Припуски при фрезеровании и шлифовании плоских поверхностей
Обработка
| Размеры поверхности, мм
| Припуск на размер при толщине заготовки, мм
| Ширина
| Длина
| От 6 до 30
| Св. 30 до 50
| Св. 50
| Получистовое фрезерование после
чернового
| До 200
|
100…250
250…400
| 1,0
1,2
1,5
| 1,0
1,5
1,7
| 1,5
1,7
2,0
| 200…400
|
100…250
250…400
| 1,2
1,5
1,7
| 1,5
1,5
2,0
| 1,7
2,0
2,5
| Чистовое
фрезерование после
получистового
| До 200
|
100…250
250…400
| 0,7
1,0
1,0
| 1,0
1,0
1,2
| 1,0
1,3
1,5
| 200…400
|
100…250
250…400
| 1,0
1,0
1,0
| 1,0
1,2
1,2
| 1,3
1,5
1,5
| Окончательное шлифование термически
обработанных и необработанных поверхностей
(1 вариант)
| До 200
|
100…250
250…400
| 0.3
0,3
-
| 0,5
0,5
0,5
| 0,5
0,5
-
| 200…400
|
100…250
250…400
| 0,3
-
-
| 0,5
0,5
0,5
| 0,5
-
-
| Шлифование после
термической обработки
(2 вариант):
черновое
чистовое
| До 200
|
100…250
250…400
| 0,2
0,2
-
| 0,3
0,3
0,3
| 0,3
0,3
-
| 200…400
|
100…250
250…400
| 0,2
-
-
| 0,3
0,3
0,3
| 0,3
-
-
| До 200
|
100…250
250…400
| 0,1
0,1
-
| 0,2
0,2
0,2
| 0,2
0,2
-
| 200…400
|
100…250
250…400
| 0,1
-
-
| 0,2
0,2
0,2
| 0,2
-
-
|
Таблица Г9 Припуски на диаметр при тонком (алмазном) растачивании отверстий
Материал заготовки
| Диаметр обрабатываемого отверстия * (свыше – до), мм
| До 30
| 30…50
| 50…80
| 80…120
| 120…180
| Легкие сплавы
| 0,2 / 0,1
| 0,3 / 0,1
| 0,4 / 0,1
| 0,5 / 0,1
| Баббит
| 0,3 / 0,1
| 0,4 / 0,1
| 0,5 / 0,1
| 0,6 / 0,2
| Бронза и чугун
| 0,2 / 0,1
| 0,3 / 0,1
| 0,4 / 0,1
| Сталь
| 0,2 / 0,1
| 0,3 / 0,1
|
*Поле допуска отверстия – Н8
Примечание. В числителе приведены припуски на предварительную обработку, а в знаменателе – на окончательную.
Таблица Г10 Припуски на обработку отверстий [23]
Обработка
|
Материал
| Диаметр отверстия, мм
| до 30
| 30…80
| 80…120
| Припуск на диаметр, мм
| Получистовое растачивание
Чистовое растачивание
| Сталь
| 0,2
0,1
| 0,2
0,1
| 0,2
0,1
| Получистовое растачивание
Чистовое растачивание
| Чугун и
цветной сплав
| 0,2
0,1
| 0,3
0,1
| 0,3
0,1
| Чистовое шлифование
| Сталь
| 0,1
| 0,1
| 0,2
| Таблица Г11 Припуски на диаметр при хонинговании отверстий [23]
Хонингование после
| Диаметр * обрабатываемого отверстия (свыше – до), мм
| До 50
| 50…80
| 80…120
| 120…180
| 180…260
| тонкого растачивания
| 0,09 / 0,06
| 0,1 / 0,07
| 0,11 / 0,08
| 0,12 / 0,09
| чистового развертывания
| 0,09 / 0,07
| 0,1 / 0,08
| 0.11 / 0,09
| 0,12
| -
| внутреннего шлифования
| 0,08 / 0,05
| 0,09 / 0,05
| 0,1 / 0,06
| 0,11 / 0,07
| 0,12 / 0,08
|
Примечание. В числителе приведены припуски на размеры для деталей из чугуна, а в знаменателе – из стали.
Таблица Г12 Припуски на обработку отверстий [23]
Обработка
| Диаметр вала, мм
| 12…18
| 18…30
| 30…50
| 50…75
| Припуск на диаметр, мм
| Зенкерование
Черновое развертывание
Чистовое развертывание
|
0,1
0,04
| 1,5
0,14
0,06
|
0,18
0,07
|
0,20
0,08
| | | | | | | |
Таблица Г13 Припуски на диаметр на внутреннее шлифование отверстий [25]
Диаметр отверстия *
(свыше – до), мм
| Припуск на диаметр при длине шлифуемого отверстия (свыше – до), мм
| До 50
| 50…100
| 100…200
| 200…300
| 300…500
| До 10
| 0,2 / 0,2
| -
| -
| -
| -
| 10….18
| 0,2 / 0,3
| 0,3 / 0,4
| -
| -
| -
| 18…30
| 0,3 / 0,3
| 0,3 / 0,4
| 0,4 / 0,4
| -
| -
| 30…50
| 0,3 / 0,4
| 0,3 / 0,4
| 0,4 / 0,4
| 0,4 / 0,5
| -
| 50…80
| 0,4 / 0,4
| 0,4 / 0,5
| 0,4 / 0,5
| 0,4 / 0,5
| -
| 80….120
| 0,5 / 0,5
| 0,5 / 0,5
| 0,5 / 0,6
| 0,5 / 0,6
| 0,6 / 0,7
| * Поле допуска отверстия – Н11
Примечание: 1. Для мелкосерийного производства припуск определяется умножением табличной величины на коэффициент 1,3.
2. В числителе дроби приведены припуски для заготовок, не подвергаемых термической обработке; в знаменателе – для закаленных заготовок.
Таблица Г14 Припуски на толщину зуба при чистовом фрезеровании шлицев [25]
Номинальный диаметр
шлицевого вала
(свыше – до), мм
| Припуск на толщину зуба при длине шлица валика (свыше – до), мм
| До 100
| 100…200
| 200…350
| 350…500
| От 10 до 18
18…30
30…50
Св.50
| 0,4…0,6
0,5…0,7
0,6…0,8
0,7…0,9
| 0,5…0,7
0,6…0,8
0,7…0,9
0,8…1,0
| -
0,7…0,9
0,8…1,0
0,9…1,2
| -
-
-
1,2…1,5
|
Таблица Г15 Припуски на толщину зуба при шлифовании шлицев [25]
Номинальный диаметр
шлицевого вала
(свыше – до), мм
| Припуск на толщину зуба при длине шлица валика (свыше – до), мм
| До 100
| 100…200
| 200…350
| 350…500
| От 10 до 18
18…30
30…50
Св.50
| 0,1…0,2
0,1…0,2
0,2…0,3
0,2…0,4
| 0,2…0,3
0,2…0,3
0,2…0,4
0,3…0,5
| -
0,2…0,4
0,3…0,5
0,3…0,5
| -
-
-
0,4…0,6
|
Приложение Д
Таблица Д1 Коды характеристики технологических документов (выборочно)
ГОСТ 3.1201-85 [61]
Характеристика технологического процесса
| Код
| 1. Вид технологического документа
Маршрутная карта
Карта эскизов
Операционная карта
|
| 2. Вид технологического процесса по методу его организации
Без указания
Единичный процесс
|
| 3. Вид технологического процесса по методу его выполнения
Без указания
Общего назначения
Технический контроль
Обработка давлением
Обработка резанием (кроме расточных и фрезерных)
Обработка резанием (расточные и фрезерные)
Термическая обработка
Получение покрытий (металлических)
Получение покрытий (лакокрасочных)
Пайка
Сборка
Сварка (газовая, дуговая)
Сварка (под флюсом, в углекислом газе и т. п.)
Наплавка
|
|
Таблица Д2 Коды операций (выборочно) [26]
Наименование операции
| Код операции
| Код 01 Операции общего назначения
|
| Обдувка
|
| Слесарная
|
| Зачистка
|
| Смазывание
|
| Дефектация
|
| Промывка водой
|
| Промывка растворителем
|
| Изолирование, защита
|
| Травление
|
| Пропитка
|
| Заливка
|
| Протирка
|
| Приготовление (клеев, флюсов и пр.)
|
| Сушка
|
| Маркирование
|
| Обезжиривание химическое
|
| Обезжиривание электрохимическое
|
| Код 02, 03 Технический контроль
|
| Контроль линейных размеров
|
| Контроль пятна контакта
|
| Контроль внешнего вида изделия
|
| Контроль технического состояния
|
| Контроль работоспособности
|
| Контроль комплектности
|
| Код 04 Перемещение
|
| Транспортирование
|
| Кантование
|
| Комплектование
|
| Сортировка
|
| Код 06, 07 Испытание
|
| Испытание на надежность
|
| Испытания механические
|
| Испытание на герметичность пневматическое
|
| Испытание на герметичность гидравлическое
|
| Код 08 Консервация и упаковка
|
| Консервация и упаковывание
|
| Код 21 Обработка давлением
|
| Высадка
|
| Обжатие
|
| Раскатка
|
| Гибка
|
| Отбортовка
|
| Раздача
|
| Калибровка
|
| Правка
|
| Код 41,42 Обработка резанием
|
| Токарная
|
| Шлифовальная
|
| Зубообрабатывающая
|
| Долбежная
|
| Протяжная
|
| Отделочная
|
| Полировальная
|
| Хонинговальная
|
| Суперфинишная
|
| Притирочная
|
| Сверлильная
|
| Расточная
|
| Фрезерная
|
| Код 51 Термическая обработка
|
| Отжиг
|
| Закалка
|
| Отпуск
|
| Код 71 Нанесение покрытий
|
| Железнение
|
| Хромирование
|
| Код 81 Пайка
|
| Лужение
|
| Пайка
|
| Код 88 Сборка
|
| Сборка
|
| Базирование
|
| Балансировка
|
| Стопорение
|
| Штифтование
|
| Запрессовывание
|
| Контровка
|
| Свинчивание
|
| Застегивание
|
| Клепка
|
| Развальцовка
|
| Склеивание
|
| Шплинтование
|
| Распрессовывание
|
| Расштифтовывание
|
| Расшплинтовывание
|
| Развинчивание
|
| Разборка
|
| Сборочно-подготовительная
|
| Слесарно-сборочная
|
| Код 91, 92, 93 Сварка, наплавка
|
| Сварка
| 9100, 9200
| Наплавка
|
|
Таблица Д3 Ключевые слова технологических переходов (выборочно) [27-31]
Ключевое слово
| Ключевое слово
| Ключевое слово
| 1. При слесарно-сборочных работах
| 2. При обработке резанием
| 3. При прочих работах
| Балансировать
| Долбить
| Осадить
| Базировать
| Зенкеровать
| Калибровать
| Гнуть
| Зенковать
| Обжать
| Закрепить
| Нарезать
| Править
| Запрессовать
| Отрезать
| Раздать
| Заточить
| Подрезать
| Лудить
| Застопорить
| Полировать
| Паять
| Зенковать
| Протянуть
| Выполнить
| Калибровать
| Рассверлить
| Приварить
| Кернить
| Расточить
| Подварить
| Контрить
| Сверлить
| Прихватить
| Клепать
| Суперфинишировать
| Сварить
| Нарезать
| Точить
| Состыковать
| Нанести
| Хонинговать
| Заварить
| Опилить
| Шлифовать
|
| Отрубить
| Цековать
|
| Очистить
| Фрезеровать
|
| Отрезать
|
|
| Править
|
|
| Притереть
|
|
| Развернуть
|
|
| Развинтить
|
|
| Развальцевать
|
|
| Распрессовать
|
|
| Расшплинтовать
|
|
| Разобрать
|
|
| Расштифтовать
|
|
| Сверлить
|
|
| Свинтить
|
|
| Склеить
|
|
| Собрать
|
|
| Соединить
|
|
| Установить
|
|
| Центровать
|
|
| Шплинтовать
|
|
| Штифтовать
|
|
|
Таблица Д4 Наименование предметов производства, поверхностей
Date: 2016-07-25; view: 356; Нарушение авторских прав Понравилась страница? Лайкни для друзей: |
|
|